2.加工条件
◆ 加工条件 ◆
・加工レベル:—
電解条件
電極材料名 | ―
|
電極形状 | 110×70mm diameter
|
電極その他 | ―
|
印加電圧 | ―
|
電流 | ―
|
電流密度 | 0mA/cm2
|
加工間隙 | 3mm
|
電解溶液材料 | NaNO3
|
電解溶液濃度 | 20wt%
|
液流量 | ―
|
液温度 | ―
|
pH | ―
|
加工時間 | ―
|
| 砥粒研磨条件
圧力 | 7.7kPa
|
送り速度 | 12mm/s
|
回転数 | 450rpm
|
圧延方向対研磨方向 |
|
砥粒材質 | ―
|
砥粒径 | ―
|
砥粒量 | ―
|
研磨材 | ナイロン不織布
|
粒度番号 | 600
|
研磨材径 | 125mm
|
|
|
◆ 装置図 ◆
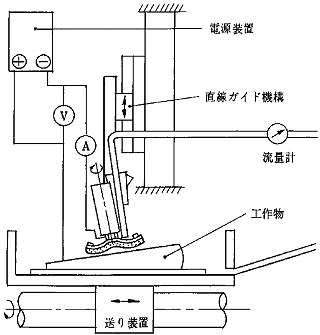
装 置
|